
Eur J Mech A Solids 26:676–687īeirow B, Kühhorn A, Nipkau J (2011) An equivalent blisk model considering the influence of the air flow on blade vibrations of a mistuned compressor blisk, Vibration Problems ICOVP 2011. Laxalde D, Thouverez F, Sinou JJ et al (2007) Qualitative analysis of forced response of blisks with friction ring dampers. In addition, the analysis results indicate that the hard coating has a significant effect on the vibration reduction of blisk.Ĭhan YJ, Ewins DJ (2012) Prediction of vibration response levels of mistuned integral bladed disks (blisks): robustness studies. The results were contrasted with the experimental data and the FEM (finite element method) results, which proved the validity of the lumped-parametric model of the hard-coated blisk. Results and ConclusionsĪ case study was carried out by taking the blisk with NiCrAlCoY + YSZ hard coating as an example, and the natural characteristics and vibration responses of the uncoated and coated blisks were calculated with the proposed lumped-parametric model. Then, the identification of parameters needed for dynamic modelling was realized using modal data obtained by experiment. Meanwhile the method of solving the natural characteristics and vibration responses was provided. The stiffness and material damping of hard coating was described by complex stiffness, and a two-degrees-of freedom lumped-parametric model and the equation of motion were established. In this paper, a method of establishing a lumped-parametric model based on the modal test data of the blisk before and after coating was proposed. The functionalities of LMDCAM are exemplified by a repair application and the near-net fabrication of a blade-integrated disk (BLISK) blade direct from the CAD model.To apply the hard-coated damping technology on the blisk with more obvious effect, it’s indispensable to develop the dynamic model of the hard-coated blisk to realize the prediction and design of the damping effect of the coating.
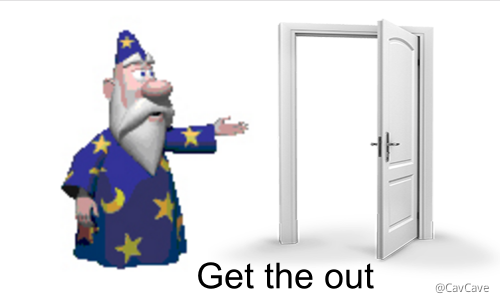
LMDCAM supports the generation of all sorts of path pattern within a layer which for example may be derived from a distortion reduction analysis. The target geometry of worn parts is derived by a best fit with the CAD model from the design stage. NURBS are only used for the reduction of data noise in the scanned data. The further step of creating a non-uniform rational B-spline (NURBS) representation of the geometry requires a major commitment in time, both in instruction and in amount of work.įor this reason the Fraunhofer Institute for Laser Technology (ILT) designed a process chain for the laser material deposition (LMD) whose CAM module termed LMDCAM, is based on a polygonal modelling approach for geometry representation. The original data format of laser scanned data is a polygonal modelling approach for surface representation. Only with this volume being available the tool paths can be programmed.

This means that first of all the actual and the target geometry have to be constructed from which the deficit volume is determined. The success of laser metal deposition (LMD) for repair or fabrication of near-net shaped metals components directly from computer aided design (CAD) solid models without use of time and cost-prohibitive conventional techniques, such as five-axis milling, linear friction welding and electro chemical machining depends on the availability of a close CAD/ computer aided manufacturing (CAM) chain.ĭistortion and defects of a worn part implies that the nominal CAD model from the design stage is no longer suitable for the representation of the part geometry. LMDCAM, Computer Aided Manufacturing (CAM) Solution for Tool Path Generation for Build-up of Complex Aerospace Components by Laser Metal Deposition (LMD)
